INDUSTRIAL DESIGN PORTFOLIO
IMMUNITY
PORTABLE FRIDGE
Challenge - Redesign a refrigerator for a new context, incorporating the principles of the UN's Sustainable Development Goals.
Concept - Portable thermoelectric cooling unit that allows vaccines and immunization equipment to be transported hands-free over uneven terrain, reducing reliance on carbon-intensive last-mile deliveries and providing accesible healthcare to those who want it.
Result - IMMUNITY is a rolling immunization kit, attached to the user by a hip strap, allowing them to carry all their personal necessities in a backpack with no interference. The device is loaded with refrigerated vaccines and all the immunization equipment required to run a mobile vaccination pop-up.
Duration 8 weeks
3rd Year Product Redesign - Studio Project
Date December 2024​​​​​
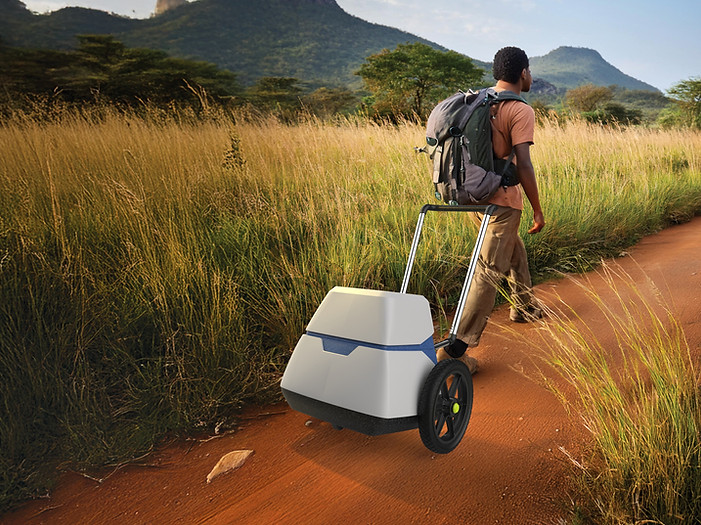
PROBLEM STATEMENT
Vaccines are not easily accessible in rural communities in Sub-saharan Africa due to transportation challenges that disconnect them from major cities. "Distance decay" is a concept that interaction between two places decreases as the distance between them increases—a significant issue when it comes to accessible healthcare.
Additionally, Africa’s reliance on imports for vaccines means that air and freight transport accounts for most of the environmental burden of distribution and the final stage of delivery — known as last-mile delivery — remains costly, inefficient, and environmentally harmful.
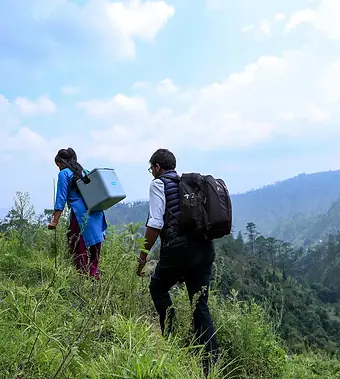
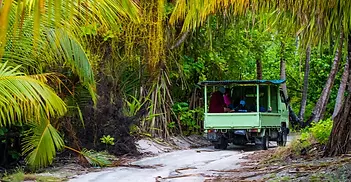


“THE CONCEPT OF “DISTANCE DECAY” SUGGESTS THAT UTILIZATION OF HEALTHCARE SERVICES DECREASES AS THE DISTANCE REQUIRED TO REACH THEM INCREASES.”
- Kaiser & Barstow, 2022
PRODUCT OVERVIEW



v2.png)

.png)
USER INTERFACE
User travels with unit by foot. Support tubing is removed using release levers. Unit can be opened, resting top compartment on fixed tubing. Secondary insulated hatch is unlocked to reveal refrigerated vaccines. Vaccines cases can be removed one at a time to be used when necessary. All clinical equipment in top compartment can be securely removed and reattached using slide fit mechanisms.
SECTIONS
IMMUNITY is comprised of three main sections: clinical equipment storage, refridgerated cooler for vaccines and waterproof battery and internal component compartment. The device can be attached to the user via hip strap, allowing them to walk freely with IMMUNITY trailing comfortably behind them.
.png)



Support Tubing - Can be removed easily using a lever. This is useful when the device is stationary and in use.
Height Adjustability - Simple snap buttons allow user to adjust the support tubing their desired height.
Battery Compartment - Waterproof battery and internal component pack ensure that weight remains at the bottom of the device.
SUSTAINABLE DEVELOPEMENT GOALS

03 - GOOD HEALTH AND WELLBEING
IMMUNITY supports SDG 3 by working to increase access to immunizations for children and adults who want it. By helping reduce preventable diseases and sicknesses, IMMUNITY contributes to creating healthier communities and improved quality of life.

10 - REDUCED INEQUALITIES
This project supports SDG 10 by striving to reduce inequalities and improve access to healthcare for rural communities in South Africa. By addressing the challenge of “distance decay”, IMMUNITY seeks to bridge the gap in healthcare access between rural and urban areas, ensuring that geographic barriers do not interfere with the quality or accessibility of care.

12 - RESPONSIBLE PRODUCTION
IMMUNITY aligns with SGD 12 by addressing the environmental and harmful impacts of last mile delivery. By using vacuum-insulated panels as its cooling mechanism, IMMUNITY is more energy efficient. Its design and manufacturing process prioritize sustainability, allowing several components and parts to be replaced or repaired using materials readily available in South Africa.
PROCESS
PRODUCT AUTOPSY
A product autopsy was conducted on the Astoria 4L mini fridge. This activity helped to learn the necessary internal components and how they are efficiently stored as well as possible insulation for thermoelectric cooling devices.

_JPG.jpg)
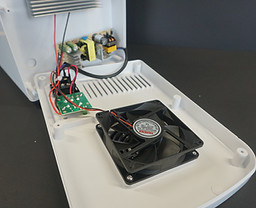
CONCEPT SKETCHES
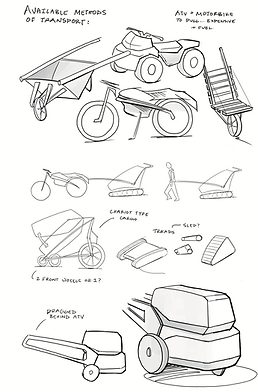.png)
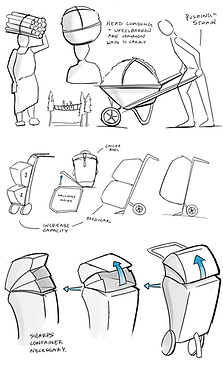





Explored various cargo transport methods, focusing on efficiency and practicality. Settled on a mobile immunization apparatus on wheels, pulled on foot. Investigated modular designs for vaccine capacity and optimized wheel types for stability and maneuverability. Transitioned from a taller design to a compact, low-profile form for better balance, accessibility, and ease of use.
TESTING + PROTOTYPES
Product testing included having users pull a weighted device (~40 lbs) on wheels behind them and then instructed to walk in a loop. Users were attached by a hip strap and again attached at shoulder height.​ User testing revealed a strong preference for a hip strap over shoulder-height attachments. Hinging attachment bars allowed fluid motion, and users reported minimal discomfort while walking, noting surprise at how much weight they could pull.
​



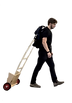





1
2
3
4
5
6
7
8
9
10
13
11
​
12
14
15
​
16
17
​
1
Polypro Connector Joints
2
Roto Molded Polypropylene Outer Casing
3
Carbon Steel Tubing
4
Injection Molded Inner Casing
5
Injection Molded Polypropylene Hinge
6
Steel Clamping Handle
7
Vacuum Insulated Layer
8
12" Spoked Wheels
9
Roto Molded Polypropylene Bottom Outer Casing
10
Custom Injection Molded Wheel Caps
11
12V Car Battery
12
Conductive Aluminum Core
Ceramic Peltier Chip
13
Aluminum Heat Sink
14
15
High Output Fan
16
Roto Molded Polypropylene Battery Compartment
17
Vent Cover
MANUFACTURING + INTERNALS
REPAIRABILITY
IMMUNITY is thoughtfully designed and manufactured to prioritize efficient repairability by using locally available materials and processes to minimize shipping and import costs for replacement parts. Carbon steel and roto molded plastics production are two industries that are well established in South Africa. The 12-inch wheels are the same size as standard children’s bike wheels, offering an affordable and sustainable replacement option.

LOOKS-LIKE SCALE MODEL
Final 1:4 scale multi material model made of high density foam, 3D printed parts, wood and found objects. The model rests on a runway to simulate the terrain that it would be used in.



CONTEXT OF USE + SCENARIO
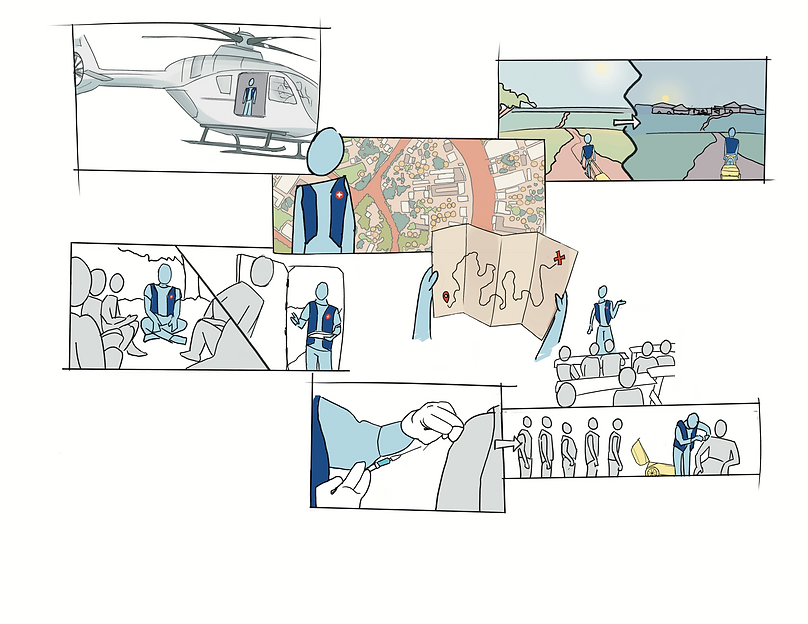
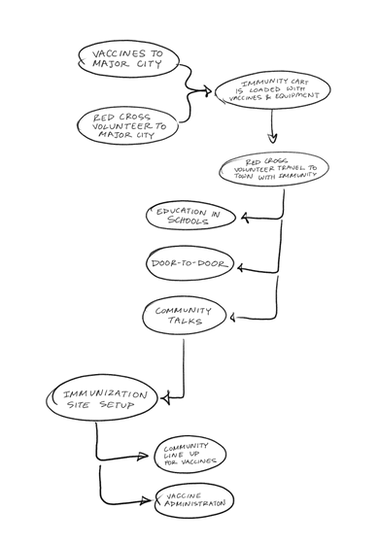