INDUSTRIAL DESIGN PORTFOLIO
ARCH
WINE RACK
Challenge - This project focused on designing a plastic, heat formed product that could be manufactured efficiently.
Concept - Arch is a wall mounted, modular wine bottle holder that is easily manufactured and assembled with minimal waste due to its sustainable design and flatpackable nature.
Result - In the world of wine racks, arch is the epitome of sophistication and functionality. Designed not only to store one’s favorite bottles, but also to create an ambiance that transforms any space into a captivating environment and enhances one’s wine-drinking experience.
Duration 3 weeks
2nd Year Design For Manufacturing Project
Date March 2024
Designed with Oscar Nikolic + Leo Causley-Bennett​​​​​
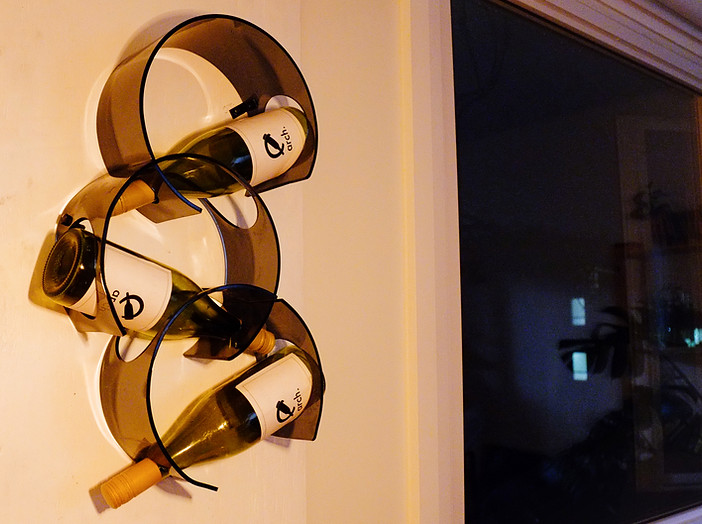
INTENT + IDEATION

ECONOMIC DESIGN
The laser cut pieces are flatpack and stackable, before and after bending. This allows for easy transportation, shipping and packing of parts. Thermoforming peach piece allows for less stress on parts and a faster and less expensive manufacturing process.
Very simplistic geometric concepts were explored in the early stages of form development. After consideration about the intent of the product, a more organic form was necessary to achieve the desired effect of an elegant and captivating design.
INITIAL CONCEPTS


USER CUSTOMIZATION
This design is modular, allowing the user to customize arch to their kitchen, and bottle collection. In restaurant settings, many more bottles to be displayed because of this feature.
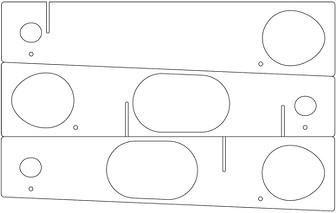
MANUFACTURABILITY + LOW WASTE
Designed for simple and cost efficient manufacturing, all three pieces can be laser cut from the same sheet of plastic with very minimal waste. Each part is thermoformed using the same jig, which saves time and makes for easily repeatable parts.

TESTING + TROUBLESHOOTING

MATERIAL ANALYSIS
Tests determined the optimal plastic to support three wine bottles without flexing, snapping, or distorting cut-outs. The chosen material was 3/16" clear acrylic.

CONNECTION LOCATIONS
Determining the placement of connection slots and cut-outs was challenging. Tracing a full-sized test bend on paper helped, and multiple test bend attempts with varying sizes refined the optimal measurements and locations.
The three bent sheets feature holes for L-brackets, allowing for wall mounting. Each bend then slots into one another to connect without stress on the parts as each is mounted to the wall individually. The brackets are strategically placed to remain hidden behind the wine bottles when the Arch is in use.
MANUFACTURING
+ ASSEMBLY


CIRCULAR CUT-OUTS
Careful geometry was used to design the bottle cut-out's shape, as bending around a large radius would distort circular cuts into ellipses. The cut shapes were therefore determined using the solidworks sheet material feature.

THERMOFORMING
The plastic was thermoformed using a conventional oven. Heating the plastic on a jig caused excessive stretching and shrinkage. Heating it flat and bending it over a cold jig proved more effective, minimizing stretching and reducing heating time.

SLOT FITTING
The three bent sheets connect using slot fits. Tests revealed the optimal slot size, accounting for shrinkage and warping, and showed that rounded edges reduce stress and prevent snapping, unlike square corners.

SHRINKAGE
An unforeseen issue was plastic shrinkage during cooling, which prevented bottles from fitting into the slots. Additional tests with varying cutout sizes (as it was impossible to calculate the shrink factor) revealed that reducing oven time minimized shrinkage.






